With a reasonably small cost of inspection and maintenance, your industrial electric motors can last for years. The following is a list of some recommended tips to help ensure reliability of operations and prevent failures over the life of your motor. See them here in our blog post.
Blog
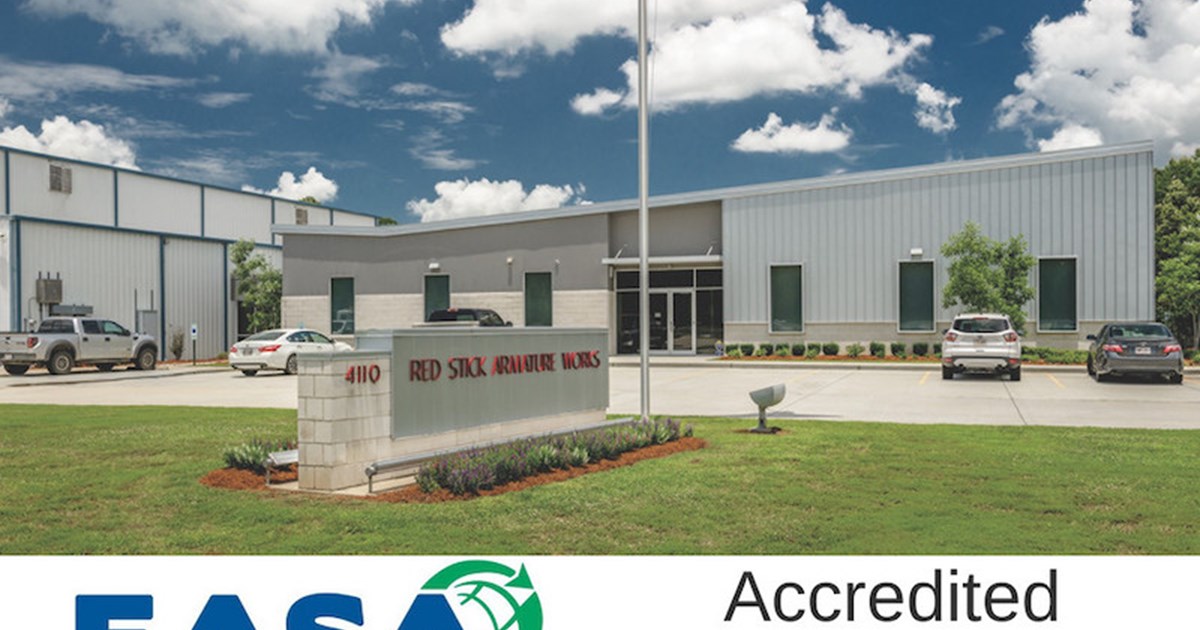
RSAW Approved as an EASA Accredited Service Center
We are pleased to announce that Red Stick Armature Works, Inc., in Saint Francisville, Louisiana, has been approved as an EASA Accredited Service Center by the Electrical Apparatus Service Association (EASA).
EASA Accreditation of Red Stick Armature means that the firm has successfully demonstrated it follows the prescribed good practices to consistently deliver quality electromechanical repairs that maintain or improve AC electric motor efficiency and reliability.

Six Key Components That Make Up Your Industrial Electric Motor
Your industrial electric motor has several critical components that enable it to efficiently and effectively convert electrical energy into the mechanical energy your plant needs to stay up and running smoothly. These include the rotor, stator, bearings, windings, air gap, and commutator. Learn more about each of them here.
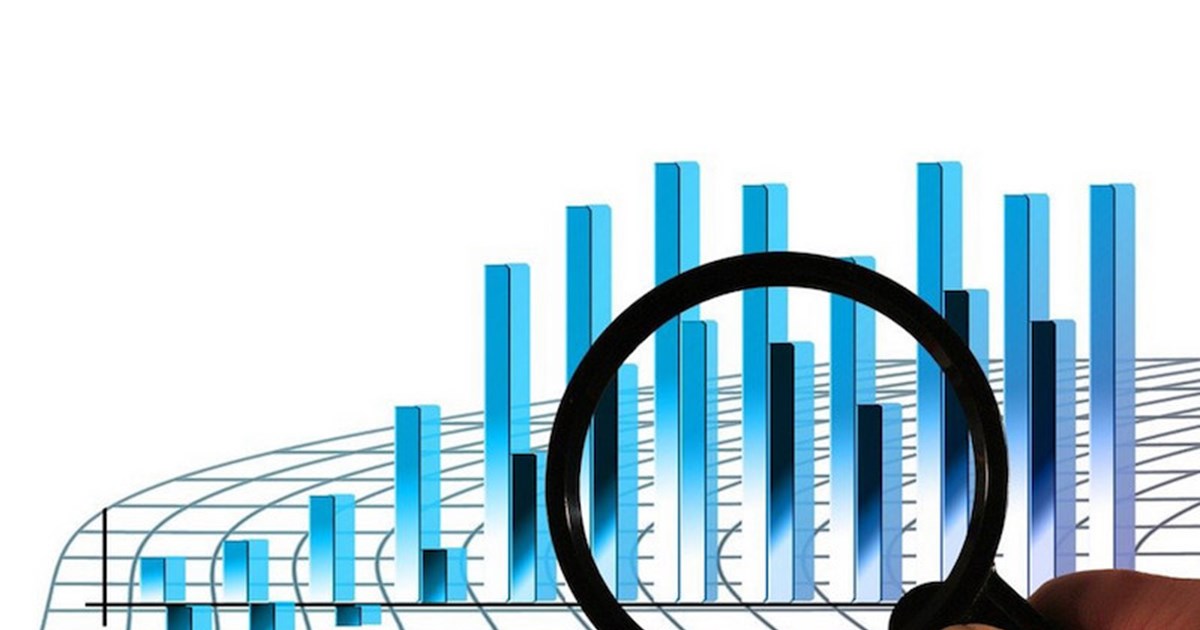
Industrial Motor Market Expected to Reach $60B by 2024
A ResarchAndMarkets.com report shares that the global industrial motors market is expected to grow to over $60B by 2024. A number of factors are driving this growth including technological advantages, MEPS, and industrial automation. All of which make industrial motors, especially High Voltage, an increasingly attractive option for a wide range of industries.

Questions to Ask When Selecting an Industrial Electric Motor Repair Company
Below is a list of questions to ask when evaluating potential industrial electric motor repair shops and service centers. The purpose of these questions is to help you identify elements that are indicative of an electric motor repair shop’s ability to deliver quality work on your motors.

Vibration Analysis and the Benefits of Predictive Maintenance
Vibration Analysis, when applied to your industrial electric motors, aims to reduce maintenance costs and equipment downtime by detecting equipment faults. It helps you identify things like unbalance, misalignment, rolling element bearing faults, and resonance conditions. It is a component of a predictive maintenance program, which is designed to help determine the condition of in-service equipment in order to estimate when maintenance should be performed. Learn more here.
RSAW Recognized for 60 Years of Industrial Electric Motor Repair, Service and Sales
On Friday, September the 20th 2019 Red Stick Armature Works celebrated 60 years of business with the ones that made it possible, our customers! It was a full day of food, music, fun and all things motors.
It was also a day when RSAW was the recipients of a wonderful presentation from Kenny Havard, West Feliciana Parish President, and honored to receive a special recognition award from Torri Buckles, Associate Director of the Louisiana Economic Development Group.
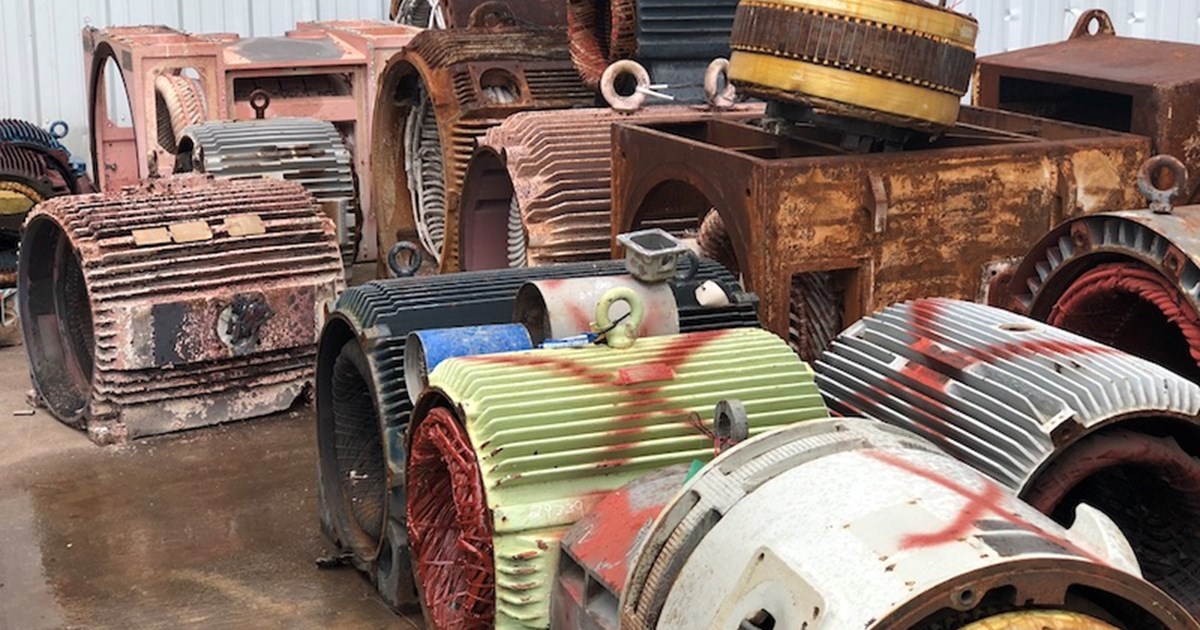
How to Decide Whether to Repair or Replace your Electric Motor?
In the EASA report “The Effect of Repair/Rewinding on Motor Efficiency”, a special section at the end is devoted to the question of whether it is better for you to repair or replace your existing electric motor. Here are 6 high-level questions you can ask to quickly decide which option might be best for you. The “Repair-replace” Business Model The process kicks-off the mome ...

Constant-Level Oiler Installation and Maintenance Tips to Extend Motor Bearing Service Life
Constant-level oilers, externally attached to motor housings, are critically important devices that provide a steady flow of oil to bearings inside the motor. In this article, learn how to keep these oilers properly filled, along with ongoing inspection and maintenance, to significantly extend bearing life.
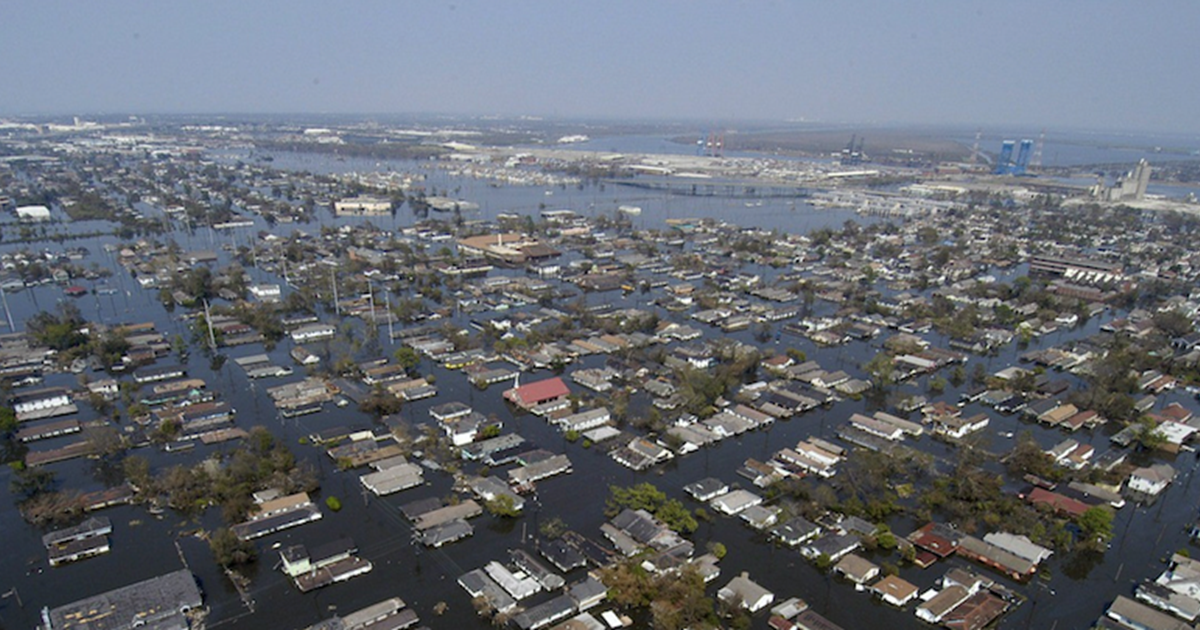
Three Critical Steps When Addressing Storm and Flood Damaged Electric Motors
In the aftermath of major storm-caused flooding to coastal and inland plant facilities, the impact of salt water, mud, and moisture can be devastating to the many different types of sizes of electric motors used in your plant.
When this happens, fast decisions must be made to get the remediation project underway and to minimize costly plant downtime.
Below are the three critical “first steps” to take if or when this ever happens to you.